Home • LIQUIDpedia • Measured values
The most important measured values for your coolant
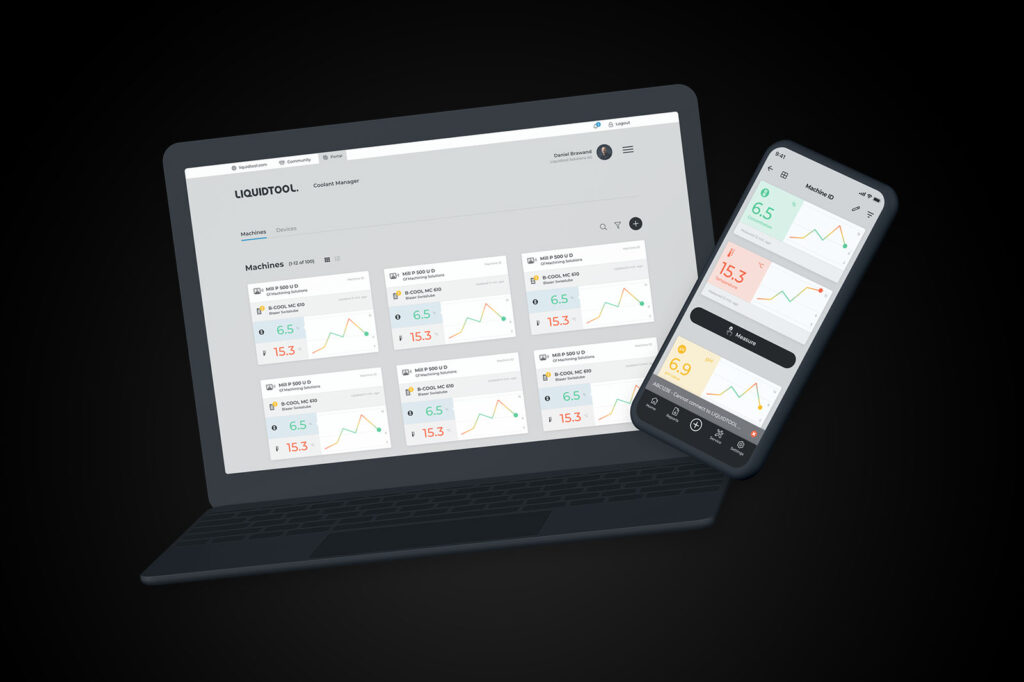
Monitor your coolant for smooth metal cutting
Metal cutting machines depend on clean coolant. While in use, however, coolant can become contaminated with dirt, waylube and hydraulic oil, metal chips, bacteria and other foreign particles.
This can have a direct impact on quality aspects such as the performance or skin compatibility of the product: Contaminated coolant that tends to foam can not only bring your machines to a complete standstill but also cause skin irritations for your employees.
This makes it all the more important to regularly monitor the following measured values and to always bear in mind the status of your coolant:
- Emulsion concentration
The most important measurement parameter indicates lubricating performance, corrosion protection, stability, foaming behavior and residue behavior. - Temperature
Keep an eye on the temperature of your coolant at all times in order to prevent the properties from changing if the temperature is too high or too low. - pH value
The development of the pH value provides valuable information about whether the coolant is contaminated. For example, an extreme drop in pH value can indicate a low emulsion concentration or a high proportion of tramp oil. On the other hand, an extreme rise can indicate possible chemical contamination with an alkaline cleaner. - Emulsion hardness
Constant emulsion hardness is key for the high quality of your coolant: High levels of hardness can lead to an unstable emulsion or to the formation of residue. - Nitrite content
By measuring the nitrite content, you can identify and avoid the risk of nitrosamine formation at an early stage.
The concentration of the emulsion and the temperature are the most important measured values that can be measured most frequently. You can regularly monitor these values automatically with the LIQUIDTOOL Sensor and document them in the LIQUIDTOOL Manager cloud-based platform solution.
You can add additional measurements directly to the platform and thus completely document the condition of your coolant.
Find out more about the benefits of automatic monitoring of coolant.